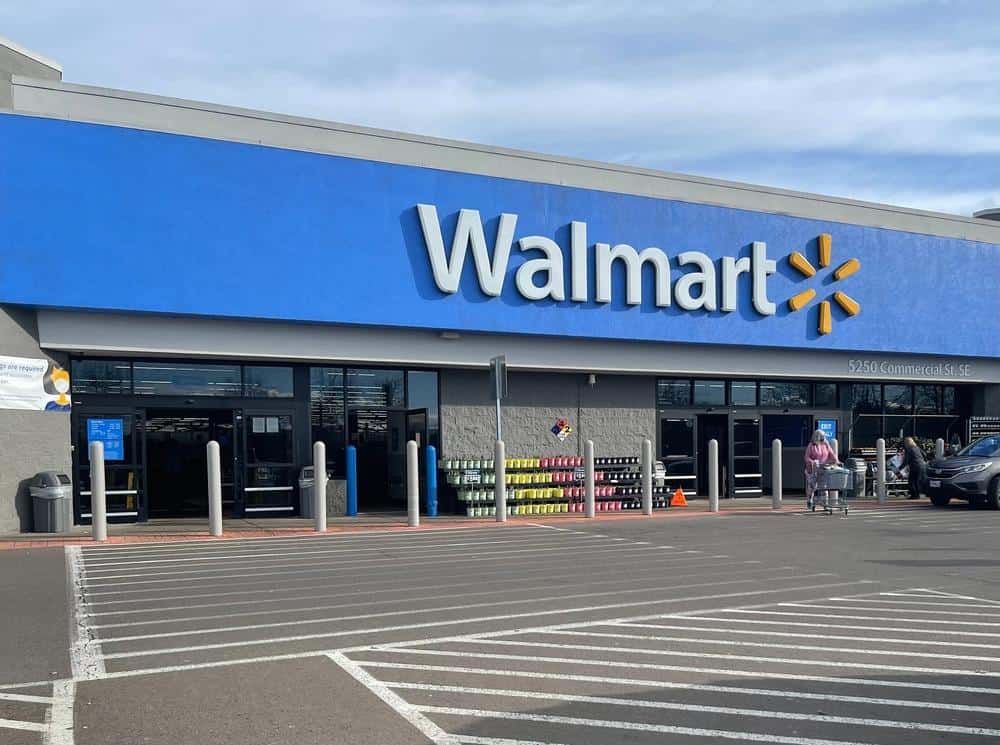
Walmart, the multinational retail corporation, is renowned for its efficient inventory management system, which plays a crucial role in its operations and overall success. The frequency at which Walmart checks its inventory varies depending on the type of products and the store. This article aims to provide an in-depth understanding of Walmart’s inventory check frequency, its inventory management methods, and the impact on its supply chain and store operations.
Walmart does not have a specific schedule for performing inventory checks across all its stores. However, they use advanced inventory management systems and technology to maintain optimal stock levels and monitor product demand. Essential items like groceries are typically restocked daily, while non-essential items are restocked based on demand and other factors.
Frequency of Inventory Checks at Walmart
Contrary to common belief, Walmart does not have a specific schedule for performing inventory checks across all its stores. However, the company uses advanced inventory management systems and technology to maintain optimal stock levels and monitor product demand.
For example, essential items like groceries are restocked daily between 10 pm and 7 am. For non-essential items such as electronics, restocking may occur at different times, depending on demand and other factors.
Advanced Methods of Inventory Management
Walmart uses several methods to manage its inventory effectively.
- Vendor-Managed Inventory Model: Suppliers access data from Walmart’s information systems, such as current inventory levels, and decide when to send additional goods to Walmart.
- RFID Inventory Scanner: This scanner can log multiple products (with RFID labels) from as far as 15 feet, improving inventory tracking efficiency.
- Walmart Inventory Management Software: This system tracks all aspects of a business’s inventory, offering real-time inventory tracking and visibility.
- AI and Automation: Walmart partnered with Brain Corp to roll out around 600 specialized scrubbers with inventory scan towers, which can distinguish between different brands and their inventory positions on the shelves.
- Augmented Reality Technology: Walmart uses an augmented reality technology called VizPick to accelerate the inventory management process, allowing workers to move products from the backroom to the sales floor more efficiently.
- Data-Driven Decision-Making: Walmart utilizes sophisticated data analytics and real-time information to make informed decisions about inventory management.
Impact on Supply Chain and Store Operations
Efficient inventory management is crucial for maintaining a responsive and efficient supply chain, ensuring well-stocked stores to meet customer demands consistently. Walmart’s inventory check frequency helps the company maintain accurate inventory records which facilitates efficient store operations.
Accurate inventory records allow Walmart to make informed decisions about replenishment, ensuring that stores have the right products in the right quantities at the right time. This, in turn, helps Walmart maintain high instock percentages, crucial for customer satisfaction and sales performance.
Handling Inventory Discrepancies
Walmart handles overstock or understock situations resulting from inventory checks by using a highly automated inventory management system and implementing strategies such as cross-docking and vendor-managed inventory models.
Leveraging Technology in Inventory Management
Walmart leverages technology and innovative strategies such as vendor-managed inventory, RFID technology, cross-docking, data-driven decision-making, and centralized inventory management systems to optimize its inventory management process and maintain its position as a leading retailer.
Conclusion
In conclusion, Walmart’s inventory check frequency plays a vital role in optimizing its supply chain and store operations. By leveraging technologies like RFID and vendor-managed inventory, Walmart maintains accurate inventory records, minimizes the bullwhip effect, and ensures well-stocked stores to meet customer demands consistently.
Frequently Asked Questions
What is the bullwhip effect mentioned in the conclusion?
The bullwhip effect refers to the tendency of fluctuations in customer demand to become more pronounced as they move up the supply chain. In other words, slight changes in customer demand can lead to significant overstock or understock situations at the retailer, wholesaler, and manufacturer levels. By maintaining accurate inventory records, Walmart can minimize this effect and ensure a more efficient supply chain.
What is cross-docking, mentioned in the section about handling inventory discrepancies?
Cross-docking is a logistics strategy where products from a supplier or manufacturer are distributed directly to a customer or retail chain with marginal to no handling or storage time. This strategy helps to reduce storage costs and improve the speed of delivery to the customer.
How does the RFID Inventory Scanner work?
RFID (Radio Frequency Identification) Inventory Scanner uses electromagnetic fields to automatically identify and track tags attached to products. These tags contain electronically stored information. This technology allows Walmart to quickly and accurately track inventory, improving the efficiency of their inventory management.
How does the vendor-managed inventory model benefit Walmart?
The vendor-managed inventory model allows suppliers to monitor the inventory levels of their products at Walmart stores. This way, the suppliers can ensure timely replenishment of their products, reducing the chances of stockouts and overstocks. This model reduces Walmart’s inventory management burden and helps maintain optimal inventory levels.
What is the purpose of using augmented reality technology like VizPick in inventory management?
The augmented reality technology, VizPick, is used by Walmart to improve the efficiency of moving products from the backroom to the sales floor. Workers use an AR device that provides visual cues to identify and pick the correct products, making the process faster and more accurate.